High-Speed Cheese Line
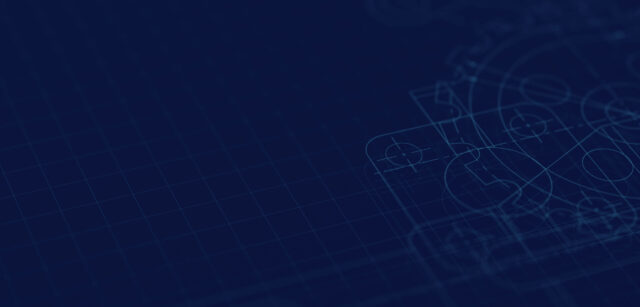
A Midwest-based dairy processor received a major new contract for deli cups with shredded cheese, requiring a significant boost in production volume and an increase in packaging integrity. While cups were regularly being produced, the process was simplistic and resulted in numerous inefficiencies. With decades of experience in the dairy industry, Sharpe was the perfect fit to design and implement a fully automated cup line.
Problem
Significantly ramping up cheese cup production, while creating a user-friendly system due to the customer’s unfamiliarity with automated cup line equipment.
The existing process could only fill 30 cups per minute and maintain in-package oxygen levels around 2%. The contract demanded speeds of 80 cups per minute and oxygen levels under 1%, a target the facility had never achieved with an automated line.
Solution
Sharpe Engineering designed and integrated a fully automated cup packaging system to meet the client’s performance, safety, and quality requirements.
Working as an extension of the client’s internal engineering team, Sharpe delivered a turnkey solution including equipment specification, layout finalization, automation, FAT coordination, and on-site commissioning.
- Vertical Tray Denester: A 12-up denester efficiently feeds cups into the line to ensure consistent product flow
- Multi-Head Scale: Accurately dispenses product weights between 4–500 grams using 24 memory buckets and a high-speed vibratory feed system
- Pneumatic Distribution System: A bucket distribution system fills four cup lanes simultaneously with conveyor indexing to ensure even product delivery
- Cup Sealing System: A dual-lane, intermittent motion system seals twelve cups per cycle under modified atmosphere, delivering low oxygen levels and high throughput
- Tamping Unit: Servo-driven system compresses cheese below the flange to ensure clean, reliable sealing
- Tray Sealer: Performs gas-flush sealing using modified atmosphere to support product freshness
- Snap-On Lidding System: Centrifugal-fed lidder applies snap-on lids and combines product flow to a single lane
- QR Code Verification: Integrated readers cross-check lid and cup QR codes, allowing automatic rejection of mismatches or defects
- X-Ray Inspection: A side-shooting X-ray system scans each sealed cup for foreign materials, with reject verification and air-blast rejection
- Controls & Automation: System-wide controls with Allen-Bradley PLCs, HMI stations, remote access (Ewon), and automated lubrication and alarm features
Sharpe oversaw the installation of the complete line, resulting in a stress-free transition into commissioning and full production.
Results
A fully automated line, providing the customer with the required capabilities to fulfill a lucrative contract.
- Maximized Throughput: Production increase from 30 to 80 cups per minute in the same facility footprint
- Elevated Food Safety: Oxygen levels reduced to <1% per package for extended shelf life
- Improved Product Traceability: Via QR code matching and rejection to reduce waste
- Efficient Product Rejection: With inline X-ray detect
- Reduced Labor Demands: Minimized staffing requirements and operator touchpoints to combat labor shortages and improve cost predictability
- Optimized Labor Efficiency: Implemented a fully automated design driven by data-backed ROI, workforce, and facility readiness
- One Partner, Total Accountability: Sharpe designed, procured, installed, and commissioned the full line
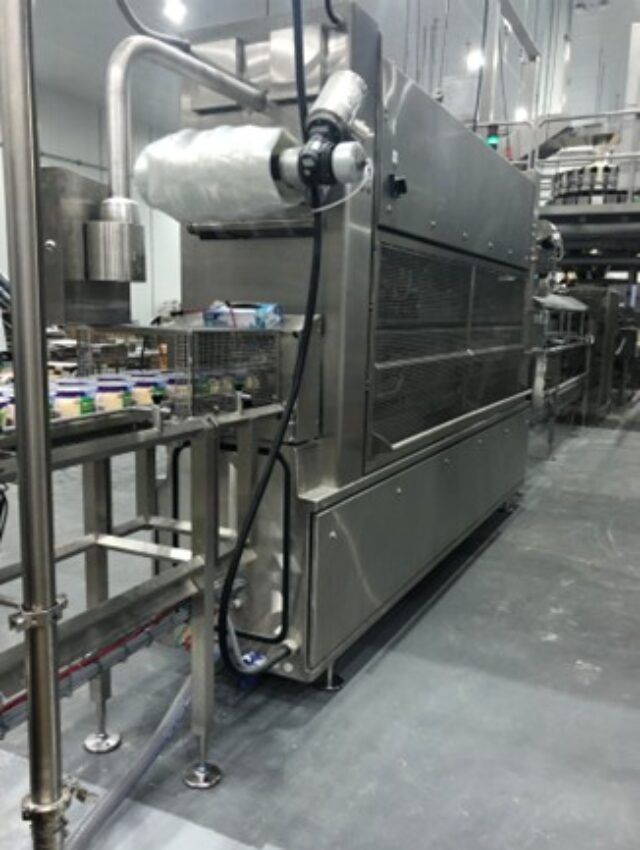
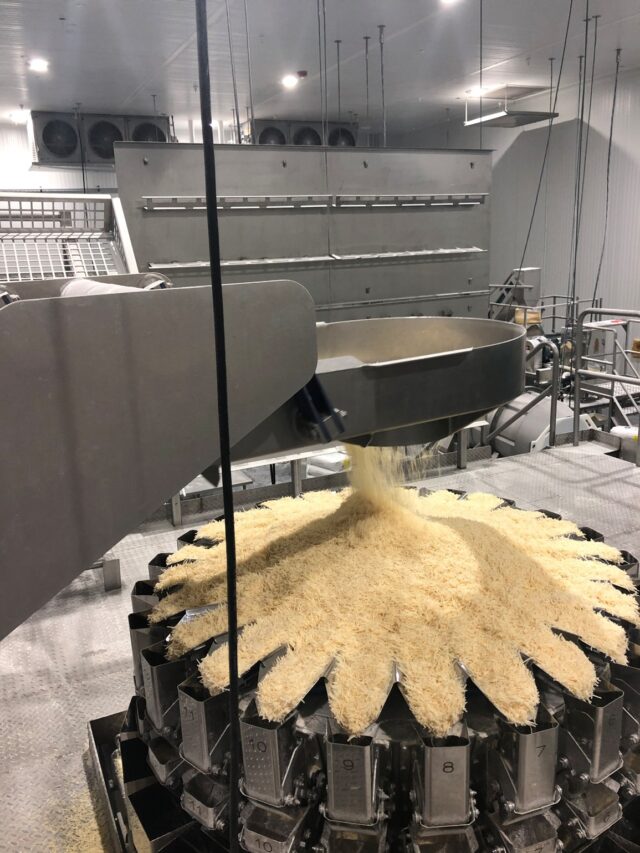
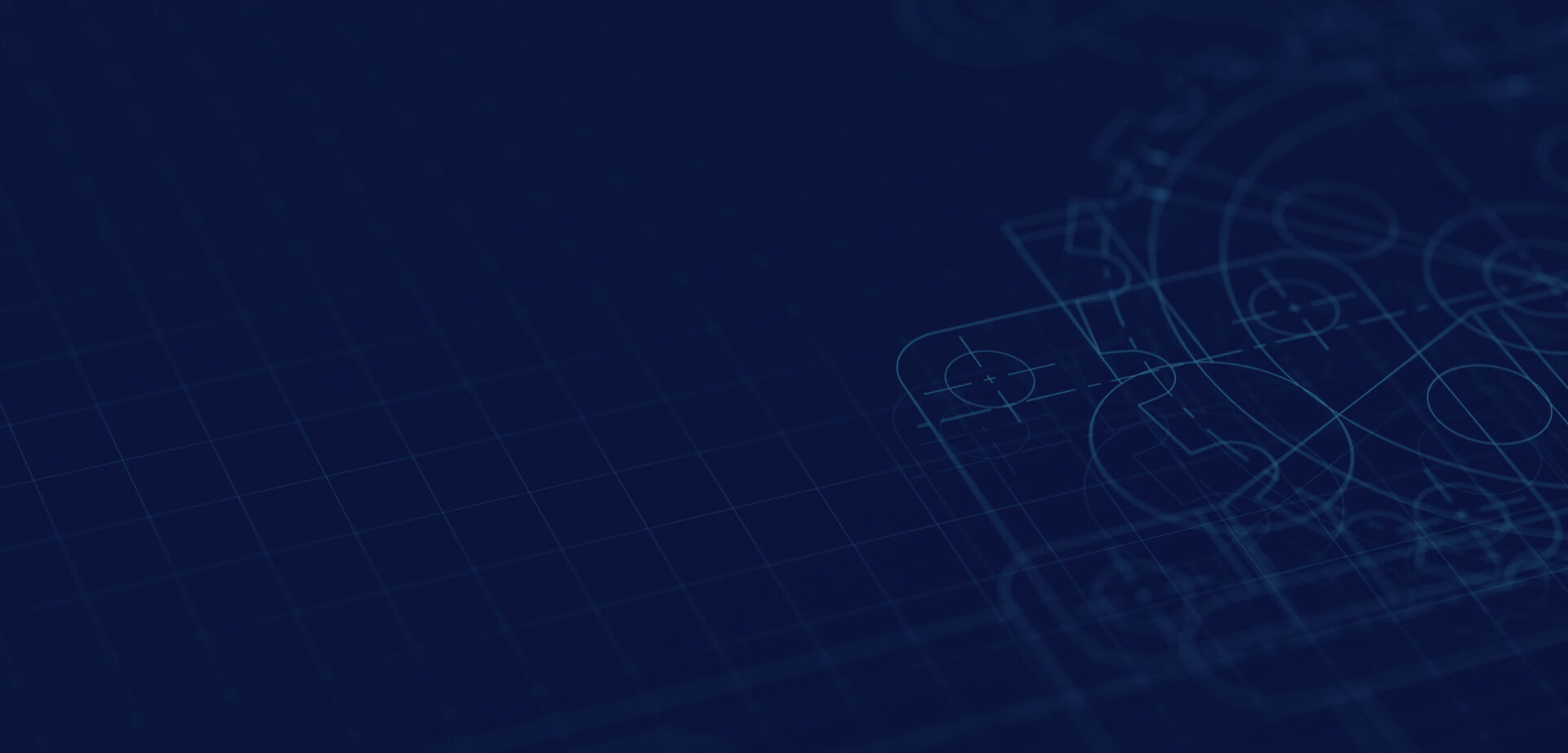
Ready to speak with our team of experts?
Feel free to give us a call, email, or fill out a short inquiry— let’s complete your project together.